
All these capabilities give you more accurate simulations and better results.īeing able to understand the immediate stresses and deformations a part undergoes is critical to structural analysis. It is also possible to account for fluid flow through pipes and heat generated from friction between parts. With Mechanical, you can read in power losses or calculated temperatures from other analysis systems or files, which means that CFD or electromagnetic simulations can be a starting point for thermal analysis. Simulating heat conduction, convection and radiation across assemblies enables you to predict the temperature of components, which can then be used to examine induced stresses and deformations. Being able to simulate contact correctly means that you can simulate the change in load paths when parts deform and confidently predict how assemblies will behave in the real world. It can simulate everything from a bonded contact that treats joints between parts as if they are glued or welded together, to contact interfaces that allow parts to move apart and together with or without frictional effects. Mechanical includes a comprehensive range of contact capabilities that enable you to account for the interactions of multiple parts. Nonlinear simulation also takes into account contact and large deflection of parts moving around relative to each other, either with or without friction. Moving beyond linear, elastic materials, you can simulate the behavior of materials as they undergo plastic or even hyperelastic deformation (materials like rubber and neoprene). Including pre-loading adds more fidelity and means that self-weighted, bolted assemblies - or even squealing brakes - can be simulated. Acoustics simulations can be carried out to understand the vibroacoustic behavior of systems, with or without structural pre-loading. Mechanical covers all your needs for dynamic analysis, including - for linear dynamics - modal, harmonic, spectrum response and random vibration with pre-stress, along with advanced solver options for rapid solutions. Seamlessly integrated multiphysics capabilities are available with our fluids and electrical solvers. Ansys Workbench enables robust connection to commercial CAD tools, providing click button design point updates. The intuitive and customizable user interface enables engineers of all levels to get answers fast and with confidence.
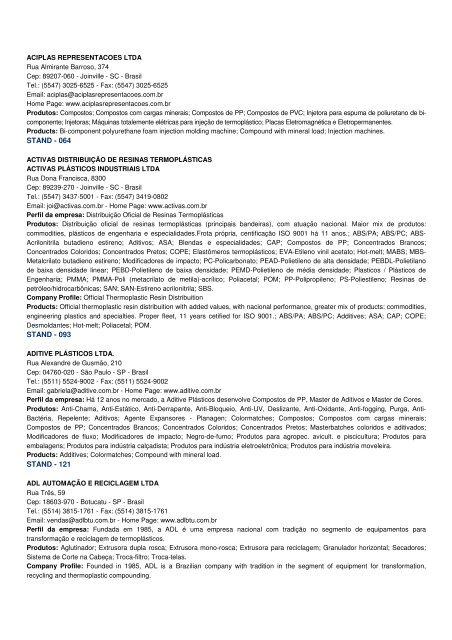
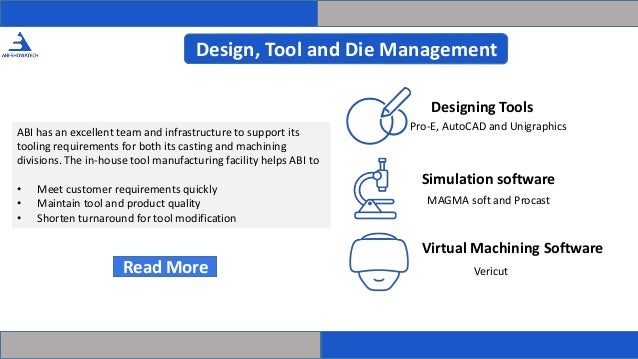
Mechanical is a dynamic environment that has a complete range of analysis tools from preparing geometry for analysis to connecting additional physics for even greater fidelity.
Magmasoft certified user full#
ANSYS® and MAGMAsoft® work collaboratively to ensure the fastest performance for simulations, ensuring faster results for more efficient computation and job turnaround times.Īs the MAGMAsoft partners in Southern Africa we have access to the full range of MAGMAsoft capabilities.Īmetex currently holds the following ANSYS capabilities: ANSYS Mechanical & ANSYS Fluent.Īnsys Mechanical is our dynamic, integrated platform that uses finite element analysis (FEA) for structural analysis.
